Por dentro da fábrica da BMW SC
A fabricação de um BMW é um processo cheio de detalhes e apenas colaboradores habilitados podem colocar o logotipo no veículo pronto

(BMW/Divulgação)
1. Minucioso
(BMW/Divulgação)
A fabricação de um carro já é um processo cheio de detalhes. Quanto mais um carro da BMW.Apenas colaboradores habilitados podem colocar o logotipo no veículo pronto, por exemplo.Além disso, todos os carros que saem da fábrica em Araquari (SC) são testados por pilotos competentes, em pista de asfalto e com obstáculos.A produção na fábrica do BMW Group em Araquari (SC) segue o princípio "build-to-stock". Ou seja, a produção de veículos no local é baseada em dados de vendas e de acordo com o volume de demanda.Confira nas imagens a seguir por dentro da fábrica da montadora.2. Treinamento
(BMW/Divulgação)
Há ilhas de treinamento dentro das áreas produtivas, algumas com foco específico no treinamento de novos colaboradores e outras para treinamento em novos veículos.3. Uniforme
(BMW/Divulgação)
Dentro da fábrica, os colaboradores usam uniforme, com seu nome bordado no lado esquerdo do peito e cores que indicam os seus departamentos. Já no escritório, a camiseta polo de uniforme é opcional, mas a maioria utiliza.4. Ao ar livre
(BMW/Divulgação)
Durante os intervalos e horários de refeição, os colaboradores podem desfrutar de uma área de lazer ao ar livre, com quadra de basquete, mesa de tênis de mesa, mesa de jogos e cancha de bocha.5. Começo de tudo
(BMW/Divulgação)
A fabricação de uma BMW começa no setor de solda de carroceria. Este setor possui duas linhas de manufatura instaladas em um espaço de 21 mil m².Aqui são soldadas algumas peças como painel lateral, portas, fecho de roda, piso do carro, fixação da suspensão, porta-malas, caixas de roda dianteira. A parede corta fogo também é soldada nesse momento – é nela que é fixado o painel que separa o motor da parte de dentro do carro, onde ficam motorista e passageiros.6. Pintura
(BMW/Divulgação)
Após a soldagem, a carroceria segue para a área de pintura. Antes mesmo da tina, ela recebe tratamento de proteção contra corrosão, seladores, e isolantes acústicos. Depois, é aplicada a pintura e o acabamento na cor desejada pelo cliente.7. Quilômetros de extensão
(BMW/Divulgação)
Para armazenar e distribuir as tintas automotivas à base de água utilizadas nesta fase, são necessários 35 quilômetros de tubulações, além de 350 quilômetros de cabos de energia e de comunicação, instalados em uma área de 23 mil m² divididos em três pavimentos. No fim da pintura, uma inspeção final minuciosa garante a excelência em qualidade.Os sistemas de transferência de tintas e outros produtos envolvem bombas e tubulações, têm pressão controlada para que haja um fluxo contínuo dos fluidos e para que as propriedades químicas não sejam alteradas.8. Armário de carros
(BMW/Divulgação)
Um sistema de prateleiras gigantes armazena e transporta as carrocerias. Este sistema faz a interligação entre as etapas de soldagem da carroceria, de pintura e da montagem e comporta até 242 unidades.O transporte é feito de forma automática: cada carroceria conta com um número de rastreamento e o sistema identifica e seleciona o próximo modelo a entrar na linha de produção.9. Sem as portas
(BMW/Divulgação)
Depois que a carroceria é pintada, ela segue para a linha de montagem. Antes de qualquer coisa, as portas são retiradas da carroceria para serem montadas separadamente. Aqui, toda a parte acústica e a forração são instaladas.10. De ponta cabeça
(BMW/Divulgação)
As linhas de montagem permitem que o carro gire em diversas posições, para auxiliar o trabalho dos colaboradores e garantir as melhores condições ergonômicas para cada etapa. A estação de giro trava o veículo de modo a permitir a rotação do automóvel para a instalação do tanque de combustível e a tubulação de freio, além de algumas proteções térmicas.11. Parte elétrica
(BMW/Divulgação)
Na sequência, acontece a passagem do chicote elétrico, que funciona como uma espécie de artéria do automóvel.É o conjunto de fios elétricos responsável pela transmissão de dados e comunicação entre os diversos módulos do veículo e a unidade central de comando, instalado no interior do veículo. São três estações que fazem a montagem dos chicotes. Aqui, o chicote é aberto e pré-posicionado no veículo.12. Painel
(BMW/Divulgação)
Os próximos itens a serem adicionados ao carro são a lanterna, acabamento interno são instalados, assoalho e tampa traseira. Depois, são inseridos a forração do assoalho e teto.Nesta etapa, o painel é colocado no interior do veículo, seguido dos vidros dianteiro e traseiro.13. Couro legítimo
(BMW/Divulgação)
Os bancos de couro são instalados um a um. Os assentos possuem exatamente o mesmo padrão de qualidade premium dos automóveis produzidos pelo BMW Group na Europa e Estados Unidos e vêm de um fornecedor “reconhecido mundialmente pela qualidade excepcional, expertise adquirida em 140 anos de história”, diz a empresa.14. Portas fechadas
(BMW/Divulgação)
Depois dos bancos, chegou a hora de colocar as portas de volta. Elas foram retiradas no início da linha de montagem, para seguirem por sua própria linha de produção.15. Quase pronto
(BMW/Divulgação)
Agora, o produto começa a ficar mais parecido com o resultado final. O veículo é erguido para se unir com o motor, a suspensão e os eixos.Na sequência, há a instalação dos para-choques e do farol dianteiro, sistema de escape e proteções inferiores.16. De perto
(BMW/Divulgação)
Aqui, detalhes do motor e eixo.17. Rodas
(BMW/Divulgação)
Os veículos são transportados para uma das etapas finais do processo de produção: a colocação dos pneus.18. Honra
(BMW/Divulgação)
Segundo a BMW, a colocação do logotipo é um momento especial na linha de produção. Apenas alguns colaboradores são habilitados a colocar o emblema da marca nos automóveis da BMW e MINI.19. Gasolina e óleo
(BMW/Divulgação)
Depois, todos os fluídos do veículo são preenchidos. Aqui, o automóvel é abastecido, programado e ligado pela primeira vez.20. Testes e mais testes
(BMW/Divulgação)
Agora com propulsão própria, o veículo se move para a área de alinhamento de rodas a laser. O laser identifica de forma mais precisa a posição e altura da carroceria em relação às rodas dianteiras e traseiras. Desta forma o processo de alinhamento é mais rápido e preciso.Depois, inicia uma série de testes. A primeira cabine é para o teste do motor. Partes eletrônicas, ABS e farol são testadas nesta etapa também.21. Passeio
(BMW/Divulgação)
Depois, os carros são levados para um passeio: 100% dos automóveis produzidos em Araquari são testados em pista de asfalto e obstáculos. Os pilotos habilitados para este teste recebem treinamento nas fábricas da BMW Alemanha. Na pista, são feitas verificações de vários componentes e funções, como o sistema de áudio e entretenimento, módulos de conexão, sensores, câmbio, dirigibilidade, ruído de vento, medição do óleo, etc. Também são testados o som, conectividade, sistema multimídia, controle de velocidade e abertura e fechamento do teto solar.22. Acabamento
(BMW/Divulgação)
O veículo ainda passa por um teste de estanqueidade. Numa cabine, ele recebe fortes jatos de água em diferentes direções, simulando uma chuva torrencial, para verificar se está bem vedado.Na linha de acabamento, a pintura é verificada, o veículo é polido e emblemas diversos são colocados, além dos tapetes e manual de instruções.Existem diversas estações de controle de qualidade durante o processo de produção, mas a auditoria de produto final é realizada no veículo completamente finalizado por equipe especializada da área de Qualidade.23. Finalizado
(BMW/Divulgação)
O carro recebe um OK final e é levado para o pátio. Será depois enviado para a concessionária, que vai entregar ao cliente. Esta foto foi feita no primeiro dia de produção da fábrica – 30 de setembro de 2014.Fonte: Exame
História da ascenção do McDonald's
O gigantesco império alimentício
Após receber uma demanda sem precedentes e notar uma movimentação de consumidores fora do normal, o vendedor de Illinois Ray Kroc (Michael Keaton) adquire uma participação nos negócios da lanchonete dos irmãos Richard e Maurice "Mac" McDonald no sul da Califórnia e, pouco a pouco eliminando os dois da rede, transforma a marca em um gigantesco império alimentício.Assista o filme completo.Ex-feirante cria rede de chocolates que fatura R$ 24 mi
Ivan Macena começou a trabalhar aos sete anos de idade. De negócio em negócio, criou uma rede de fondue saudável que já possui 80 unidades

Ivan Macena, dono da Fábrica Di Chocolate: (Foto)
História de vida
Macena acumulou diversos empregos e empreendimentos até chegar à Fábrica Di Chocolate. Ele começou a trabalhar vendendo frutas com os vizinhos em feiras, por volta dos sete anos de idade.Após cerca de três anos como feirante, conseguiu o primeiro emprego retirando lotes de borracha para carros, e depois trabalhou em uma vidraçaria.Aos 15 anos de idade, Macena participou de seu primeiro negócio, com a mãe e a irmã: uma rotisseria em São Bernardo do Campo (São Paulo), para venda de pratos congelados. Elas faziam as comidas e ele era responsável pelas vendas aos fins de semana – nos dias úteis, trabalhava em um escritório.“Éramos em dez irmãos, e os mais velhos já tinham de trabalhar. Queria ganhar meu dinheiro, e ficava pensando em como trabalhar para isso”, conta o empreendedor. “Depois, já como funcionário, vi o quanto eu conseguia produzir – e queria trabalhar para mim mesmo. Por isso, sempre tentei conciliar o emprego com um negócio próprio.”Foi assim durante cinco anos. Quando Macena tinha 21 anos de idade, montou um estande de adesivos, chaveiros, embalagens e presentes na rua 25 de Março. O negócio durou três anos.“Mesmo assim, percebi que negócios assim tinham uma sazonalidade muito grande, e eu queria algo mais estável. Enquanto não via uma oportunidade negócio, resolvi aproveitar uma proposta de emprego.”Aos 24 anos de idade, ele recebeu um convite para trabalhar no Grupo Votorantim. Ficou nove anos na gigante, fazendo contratos de compra e logística.Depois de passar quase dois anos em uma multinacional alemã, Macena aceitou uma terceira proposta de emprego em logística e suprimentos, da multinacional Tigre. Dessa vez, teve de se mudar para Joinville (Santa Catarina).O ano era 2002. A família não se adaptou muito bem à nova cidade: a esposa de Macena havia acabado de se formar em Direito e encontrava dificuldades para se estabelecer no mercado.Pensando em um negócio para os dois, marcou uma conversa com o administrador de um shopping em Joinville. A ideia era montar uma loja, mas ouvir pessoas conversando na recepção do local enquanto aguardava o administrador mudou os planos do empreendedor. Elas reclamavam que só havia uma loja que vendia chocolates no shopping todo.Fábrica Di Chocolate
Macena pensou no que havia acabado de ouvir dos consumidores, e também no fato de que costumava fazer fondue para seus amigos.Assim que a reunião com o administrador começou, ele revelou seus planos de abrir um quiosque de foundue express. Após alguns dias, Macena enviou o projeto de quiosque e recebeu, como resposta, um prazo de 20 dias para instalar o negócio.A Fábrica di Chocolate começou com esse primeiro quiosque, no ano de 2003. “Fiquei com esse negócio por três anos trabalhando de noite, enquanto lidava com o emprego no horário comercial.”Nesses três anos, muita gente perguntava se Macena não queria franquear seu quiosque. Por isso, o empreendedor estudou o mercado e se associou à Associação Brasileira de Franchising (ABF).Macena recebeu a autorização para franquear apenas em 2006, com a elaboração de um plano de negócios voltado a quiosques franqueáveis.A família já conseguia viver da renda do quiosque, e então o empreendedor largou de vez o emprego para focar na franqueadora.“Eu mesmo fiz o plano e comecei a divulgar na internet, atendendo os interessados no shopping mesmo”, conta. “As primeiras franquias apareceram em Curitiba e Salvador, e aí foi indo. Quando vendi a quarta, comecei a me estruturar: contratei funcionários e montei um escritório.”Macena não conhecia o tamanho do mercado até então – e só ao se associar à ABF percebeu que outros três negócios apostavam também no fondue express.“Se você não tiver um conhecimento profundo do mercado antes, você não conseguirá criar um negócio de sucesso franqueável, com boa formatação”, defende o empreendedor. “Estávamos em quarto lugar, e hoje somos líderes no mercado.”Para se diferenciar, Macena fez uma parceria com uma empresa belga para produzir seu chocolate.“Nosso chocolate não tem glúten nem gordura trans e hidrogenada. Com isso, pudemos unir frutas a um chocolate que só tem gordura por conta do leite que vai em sua formulação, gerando um fondue saudável e com muito sabor. A gente evita ao máximo trabalhar com ingredientes pesados, como o leite condensado.”O fondue representa, hoje, 75% das vendas nas unidades da Fábrica di Chocolate. O ticket médio fica em cerca de 12 reais, em uma estratégia de negócio que foca nas classes B e C.Fonte: ExameBrasil começa a sair da recessão
Três indicadores apontam que o Brasil começa a sair da recessão; veja quais são:
Crescimento previsto por Serasa Experian, Banco Central e FGV varia entre 0,9% e 1,19%
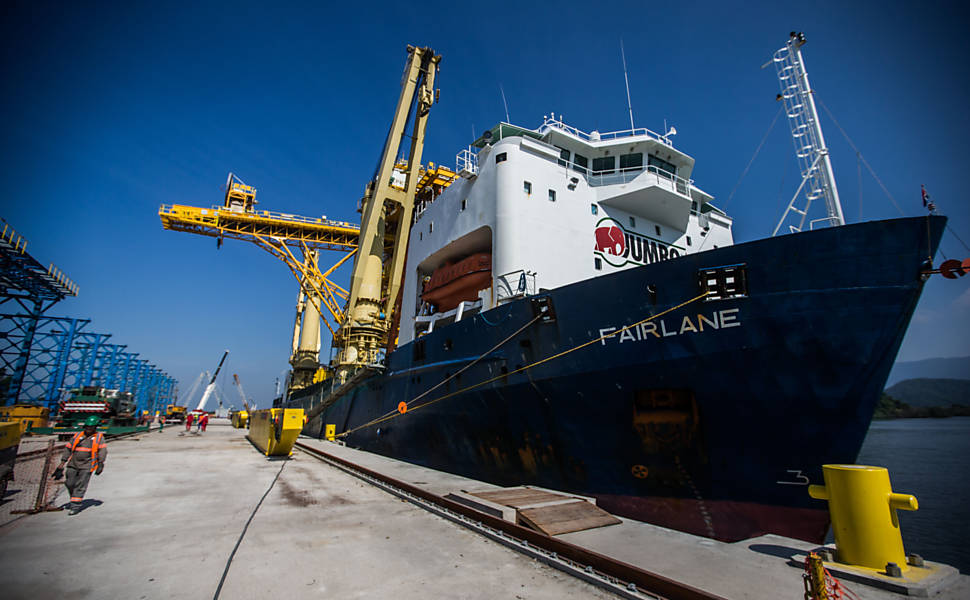
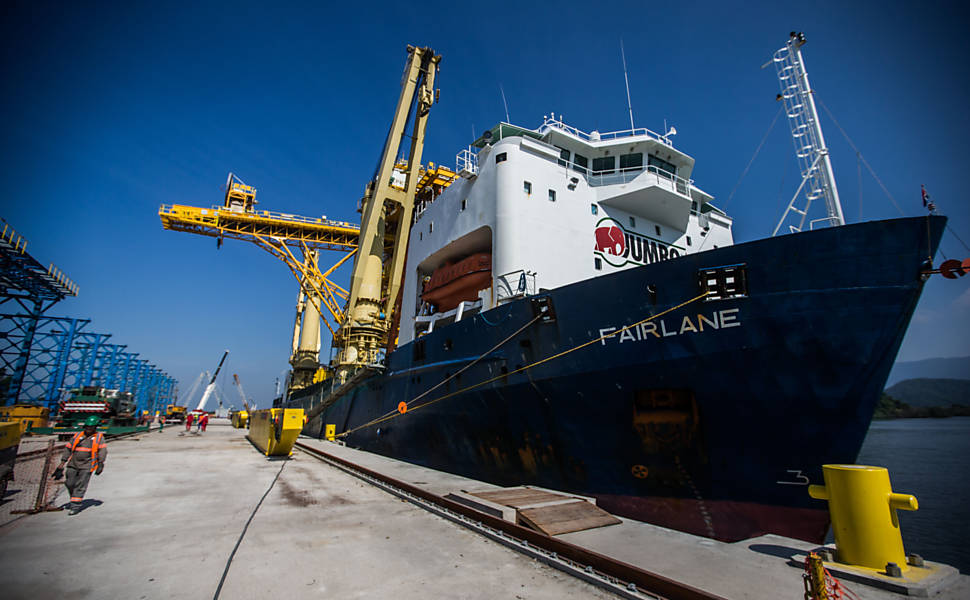
O que esta padaria de 92 anos faz para crescer
O Bologna foi fundado em 1925 e já está em sua quarta geração de donos. Diante da crise, eles tiveram de se reinventar - mas sem perder a tradição

Fachada do restaurante, rotisseria e padaria Bologna: negócio passou a funcionar 24h para aumentar seu faturamento (Bologna/Divulgação)
Reformas e tradição
O restaurante Bologna foi criado pelo empreendedor Antonio Trombetti, na região do Brás, em 1925. Depois de alguns anos no Anhangabaú, o negócio mudou-se para a rua Augusta em 1959, onde permanece até hoje. Também virou uma rotisseria – negócio de comida para a viagem.

Foto da rotisseria Bologna, em tempos antigos (Bologna/Divulgação)


O Bologna, depois da reforma feita em 2012 (Bologna/Divulgação)
Aproveitando a noite na Augusta
Mesmo que a reforma feita em 2012 tenha evitado envidar-se em plena crise econômica, o Bologna ainda tinha de procurar formas de aumentar o faturamento.Por isso, há um ano e meio o negócio adotou o regime de funcionamento de 24 horas por dia (exceto aos domingos, quando a casa fecha à meia-noite). A estratégia só funcionou a região possui uma vida noturna muito intensa e não há muitos locais para comer uma boa refeição na madrugada, diz Wagner.“Tem muita empresa que abre 24 horas, mas não tem ponto para tal. Aí só se afunda ainda mais, porque as despesas sobem e as receitas não crescem na mesma proporção.”“A gente sentiu que, na região que estamos, nossos clientes pediam isso. Eles perguntaram quando iríamos funcionar na madrugada, e resolver abrir em alguns dias específicos, como feriados e fins de semana. Como vimos sucesso, resolvemos atender de vez os pedidos”, completa Gleusa.Para isso, o Bologna designou uma equipe apenas para o horário – juntando todos os turnos, 57 funcionários trabalham no local. Enquanto até a meia-noite todos os pratos são servidos, na madrugada não há pratos: há lanches, pizzas, salgados e sopas, por exemplo.

Coxinhas cremosas vendidas no Bologna (Bologna/Divulgação)
Movimento atual e planos futuros
O próximo passo é introduzir a cozinha também na madrugada, a partir dos pratos mais demandados dos clientes. O Bologna já recebeu proposta de vender os lanches, salgados e sorvetes por meio de lojas de shopping, mas ainda não está nada acertado.“Não cogitamos abrirmos essas lojas em plena crise. O que acontecer com o país daqui para frente irá nos convencer ou não da ideia”, diz Wagner.Fonte: Exame5 conselhos do criador do Habib’s
Alberto Saraiva, criador do Habib's e do Ragazzo, acredita que amar os clientes é a base para o sucesso de uma empresa
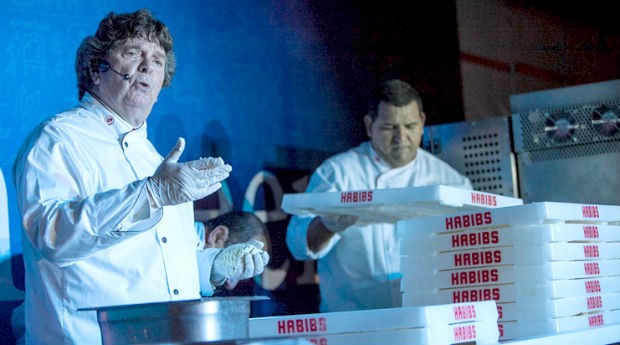
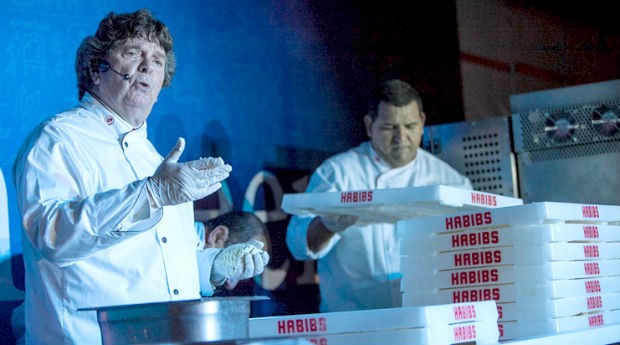
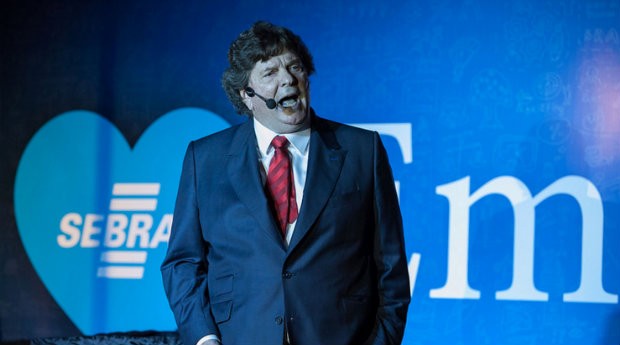
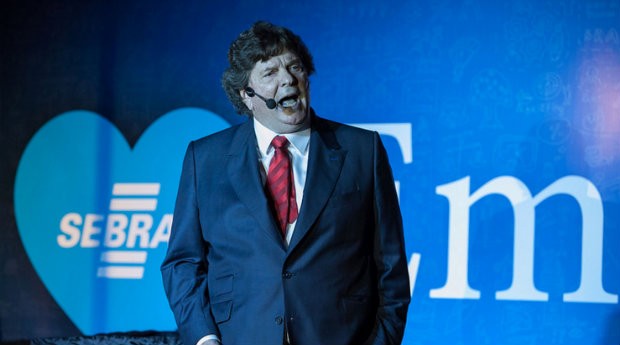
Clóvis Tramontina e Júnior Durski
Histórias que deram origem a duas marcas de sucesso
Líderes da empresa de utensílios domésticos Tramontina e da rede de restaurantes Madero contaram como conseguiram romper fronteiras e se destacar no mundo empresarial




Dudalina completa 60 anos de história


Cervejaria abre fábrica na "cidade mais alemã do Brasil" e fatura R$15 milões
A Schornstein foi fundada em 2006 por três descendentes de alemão na cidade de Pomerode, interior de Santa Catarina
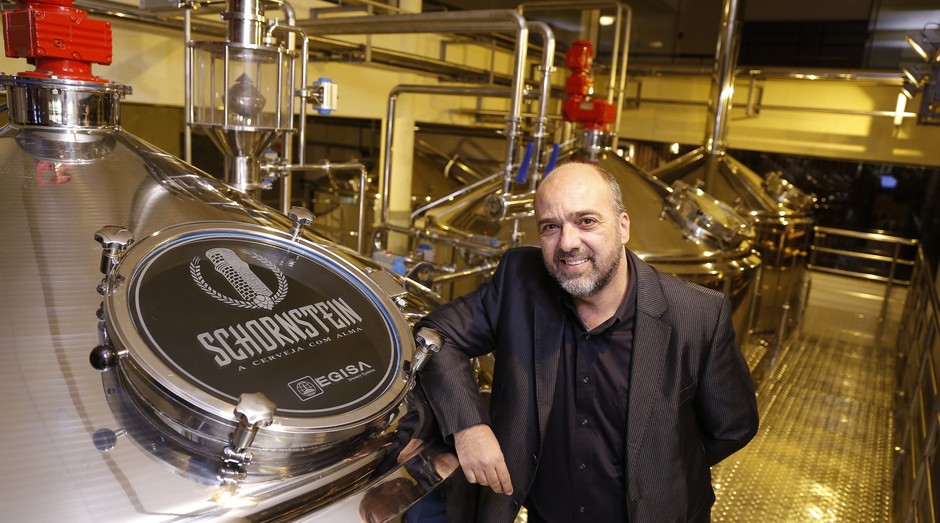
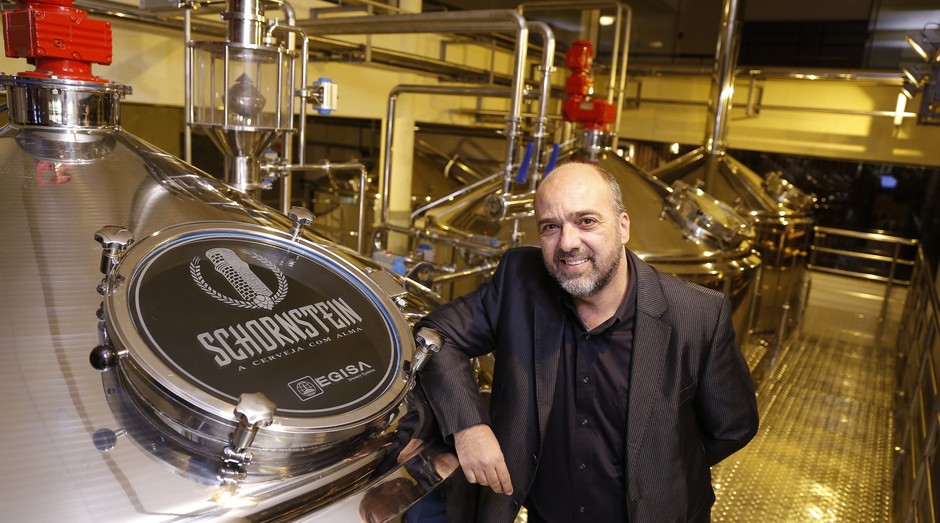
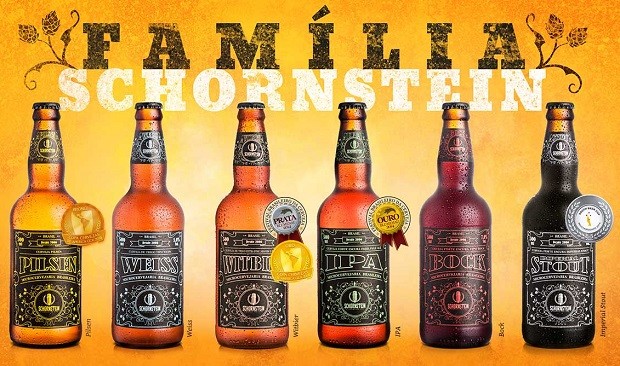
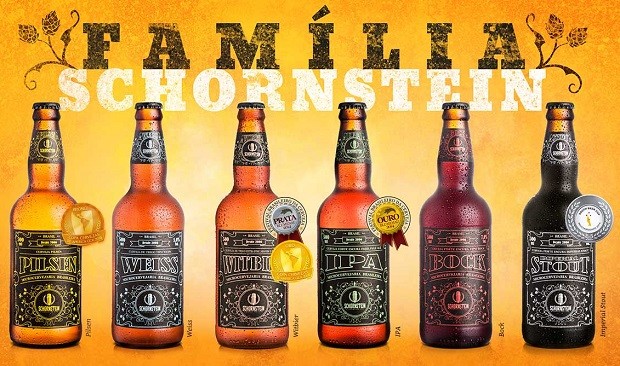